Comprehending What is Porosity in Welding: Causes and Solutions
Comprehending What is Porosity in Welding: Causes and Solutions
Blog Article
Porosity in Welding: Identifying Common Issues and Implementing Best Practices for Prevention
Porosity in welding is a prevalent problem that typically goes undetected until it causes considerable troubles with the stability of welds. In this conversation, we will certainly check out the crucial factors adding to porosity development, analyze its detrimental impacts on weld efficiency, and discuss the best practices that can be adopted to minimize porosity event in welding procedures.
Usual Root Causes Of Porosity

Using dirty or wet filler products can introduce pollutants into the weld, adding to porosity concerns. To reduce these common reasons of porosity, thorough cleaning of base metals, appropriate securing gas choice, and adherence to optimum welding specifications are crucial techniques in attaining top quality, porosity-free welds.
Influence of Porosity on Weld Top Quality

The presence of porosity in welding can considerably endanger the architectural stability and mechanical buildings of bonded joints. Porosity creates gaps within the weld steel, weakening its total strength and load-bearing capacity.
Welds with high porosity degrees have a tendency to show lower impact strength and decreased ability to warp plastically before fracturing. Porosity can restrain the weld's capacity to effectively transmit pressures, leading to premature weld failure and potential security risks in vital frameworks.
Ideal Practices for Porosity Avoidance
To improve the structural integrity and high quality of welded joints, what certain procedures can be implemented to decrease the incident of porosity throughout the welding procedure? Making use of the correct welding technique for the specific material being welded, such as changing the welding angle and weapon setting, can better stop porosity. Routine assessment of welds and prompt removal of any kind of issues identified during the welding process are vital methods to prevent porosity and generate top quality welds.
Significance of Proper Welding Techniques
Executing appropriate welding strategies is vital in making certain the architectural honesty and high quality of bonded joints, building on the foundation of reliable porosity prevention measures. Welding techniques directly influence the overall strength and durability of the welded framework. One essential aspect of appropriate welding techniques useful content is preserving the correct warmth input. Too much warmth can bring about boosted porosity due to the entrapment of gases in the weld swimming pool. Alternatively, inadequate warmth may result in insufficient blend, developing prospective powerlessness in the joint. Additionally, utilizing the appropriate welding criteria, such as voltage, existing, and take a trip speed, is vital for accomplishing audio welds with minimal porosity.
Moreover, the selection of welding procedure, whether it be MIG, TIG, or stick welding, ought to align with the specific requirements of the job to make certain optimal outcomes. Correct cleansing and prep work of the base steel, in addition to selecting the right filler material, are also crucial components of skilled welding techniques. By sticking to these finest techniques, welders can lessen the risk of porosity formation and create high-quality, structurally audio welds.
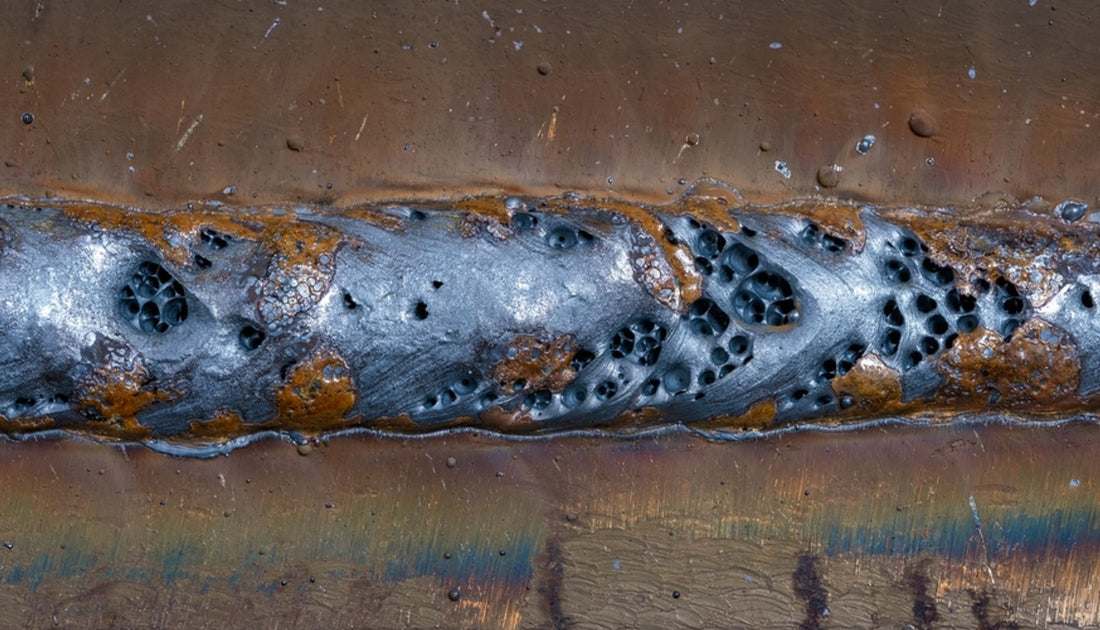
Testing and Quality Assurance Steps
Quality assurance actions play an important function in validating the honesty and dependability of welded joints. Evaluating treatments are essential to find and avoid porosity in welding, ensuring the strength and longevity of the final item. Non-destructive testing techniques such as ultrasonic testing, radiographic testing, and aesthetic examination are commonly utilized to recognize potential issues like porosity. These strategies enable for the analysis of weld top quality without site web compromising the stability of the joint. What is Porosity.
Post-weld inspections, on the other hand, analyze the last weld for any kind of issues, including porosity, and verify that it meets defined standards. Carrying out a comprehensive quality control strategy that consists of detailed testing treatments and inspections is vital to reducing porosity concerns and making certain the total go to my blog quality of welded joints.
Final Thought
Finally, porosity in welding can be an usual issue that impacts the high quality of welds. By determining the usual sources of porosity and implementing ideal techniques for prevention, such as appropriate welding methods and testing steps, welders can ensure premium quality and trusted welds. It is vital to focus on prevention approaches to minimize the incident of porosity and keep the honesty of bonded frameworks.
Report this page